The future of CNC manufacturing is characterized by an increasing level of complexity. More product variants, changes in demand, evolving technology, lead time requirements and cost pressures all highlight the need to achieve production resilience – the combination of flexibility and efficiency.
To summarize, the five essential points on the future of CNC manufacturing are:
1. Shift towards ‘high-mix, low-volume’ manufacturing
2. More ‘done-in-one’ machining with multi-purpose CNC machines
3. More automation of CNC machines as well as CNC supportive processes
4. Production planning and resource management software enable full production control
5. Megatrends of sustainability, manufacturing re-shoring and availability of workforce shape the industry
The future requires the adoption of new capabilities and cannot face additional purchases of new machines. The nature of manufacturing work has also changed dramatically.
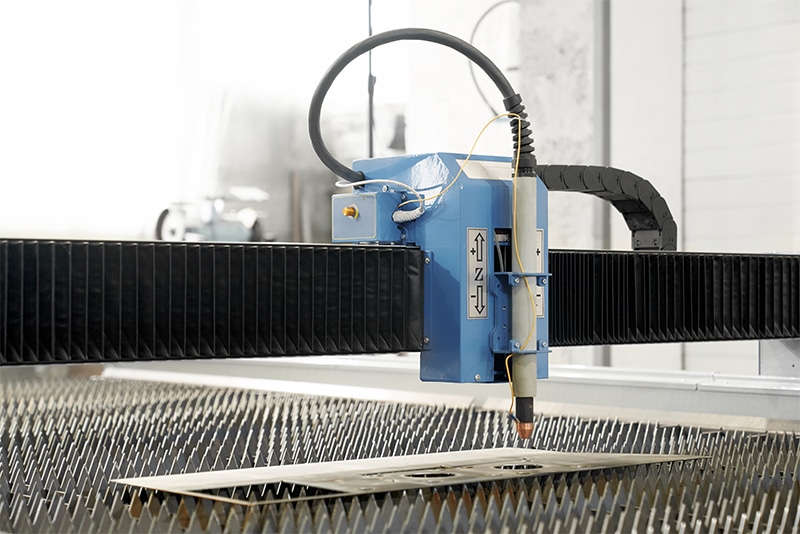
The Future on Three Levels
เรามาทบทวนลักษณะและแนวโน้มของการผลิต CNC ในอนาคตสามระดับ ได้แก่ อุตสาหกรรมทั้งหมด ผู้ผลิตรายบุคคล และพื้นโรงงาน โปรดทราบว่าแนวโน้มส่วนใหญ่มีผลกระทบในหลายระดับนอกเหนือจากที่วางไว้ด้านล่าง
1. The manufacturing industry
Customer value and profitability challenges.To stay competitive, manufacturers need constantly to deliver more in terms of product features, quality, selection, price, delivery time, service and more. For individual manufacturers, this means increasing high-mix, low-volume production and creates a decisive challenge for profitability, driving the need for developing better ways to manufacture. Especially in the case of more advanced machining applications, manufacturing is increasingly a source of competitive advantage for industrial companies.
Sustainability is of fundamental importance for the future of our planet and the humanity. Sustainability can be boiled down to three essential perspectives also known as triple-P for people, planet and profitability. In order to fight the climate change by reducing CO2 emissions, the manufacturing industry needs higher resource efficiency, more timely production, less waste and the adoption of the circular economy. This development simply isn’t possible without automation that also helps companies to do better business and makes manufacturing jobs more meaningful and safe. For societies at large, a competitive manufacturing industry supports the development of healthy national economics enabling people’s well-being in the long run.
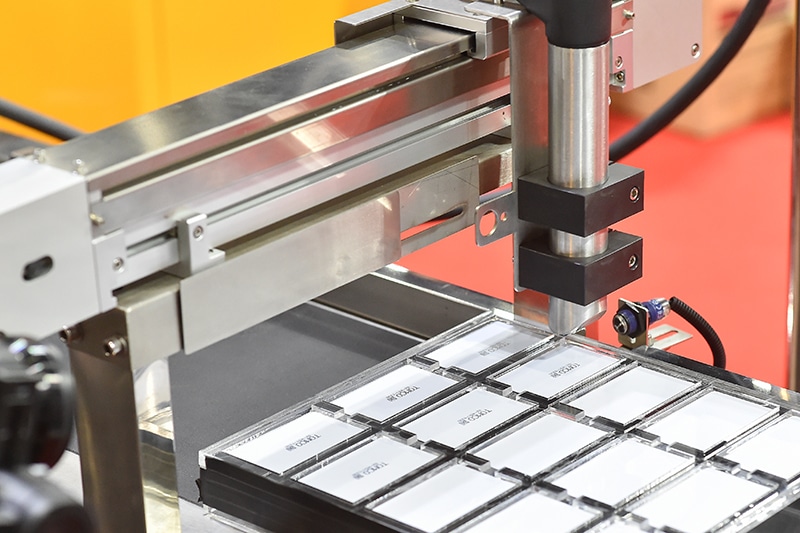
Changes in globalization, population and production jobs from the spread of the COVID-19 virus clearly highlighted Global value chains where manufacturing is far from final product markets present challenges and risks. Additionally, an aging population and the desire of young people make it challenging to find skilled personnel for manufacturing jobs. which limits the growth of the company Young people may view manufacturing as an uninteresting industry. But this is a serious misunderstanding.
2. Manufacturing companies
The requirements on industrial manufacturers are growing, leading to high-mix-low-volume production. Connections between factories also become more transparent
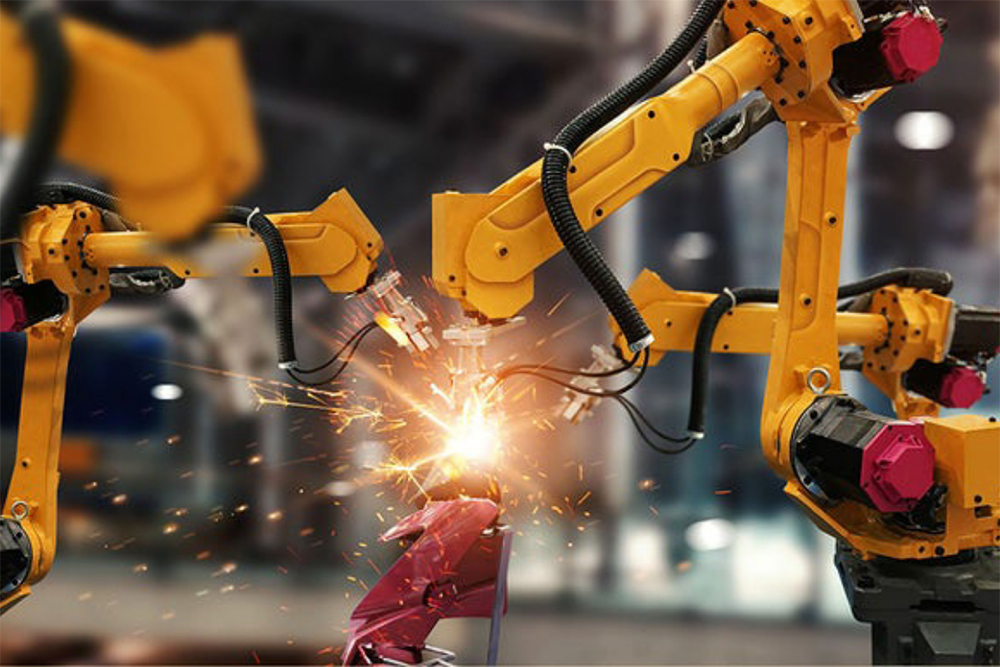
- Increasing customization and variants. Industrial products are getting more complicated and tailored per need. The average lifespan of a workpiece in production is also getting shorter and more uncertain. Combined with growing lead time pressures the requirements for manufacturing to combine efficiency with flexibility and transparency becomes essential.
- Constant changes in the markets can mean, among other things, overall demand volatility or changes in the demand mix requiring fast adaption. This calls for manufacturing resilience. Shorter planning cycles can be due to contractual causes meaning that machine shops – or product owners – don’t know what they will be manufacturing after a month or two. This is also a symptom of the above drivers.
- Quality and traceability requirements are getting more demanding not just in aerospace but in the machine building industries in general. Never-ending pressure to cut cost and reduce tied capital is always present, calling for companies to find new ways to drive manufacturing profitability and efficient use of capital. This is especially true when manufacturing re-shoring is happening.
- Factories are getting more inter-connected and as manufacturing almost always happens in some network, transparency and data sharing are a must for efficiency and flexibility. Enabled by manufacturing operations management software, in the world of hyper-connected factories one could know when the parts needed in your assembly are arriving and you’d also know – without separately asking or checking – that the necessary quality features and checks are fulfilled.
3. CNC machining & shopfloors
Automated, multi-purpose CNC machines popularize. Supported by process and data system integration, production planning software (like Fastems MMS) enable production control
Emphasis on the “Finish work in one machine” has resulted in multi-purpose machines becoming a hot hit. Using this means that the machining process can be completed with less clamping. And often in the same machine, such as lathes, milling machines with 4 or 5 axes can meet more workpiece design requirements. And decide the right production method with more accuracy than ever before.
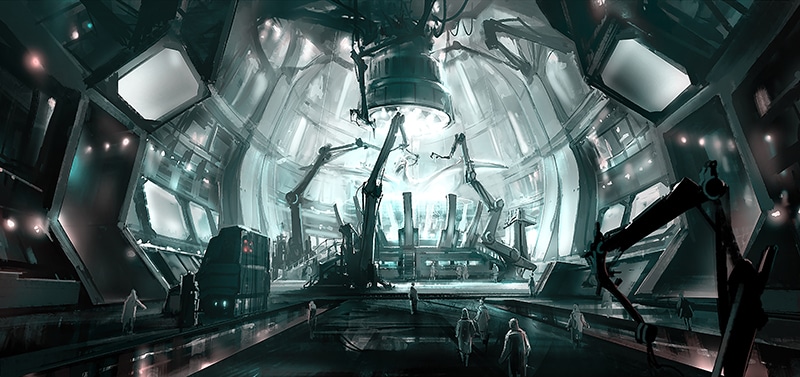
Many additional devices that support CNC Machining, such as washing, measuring, marking, finishing, etc., are integrated into the automation system for higher productivity and productivity. There is a more stable process. manage complicated things All of this can be done by software.
Challenges in production planning and production resource management especially the matter of information Collaboration between people, software and machines. Efficient connectors are required. For that role it used to be Excel, but it currently doesn’t handle the complexity as well as specialized production planning software.
References : pwat.co.th, www.fastems.com
The Future of CNC Manufacturing